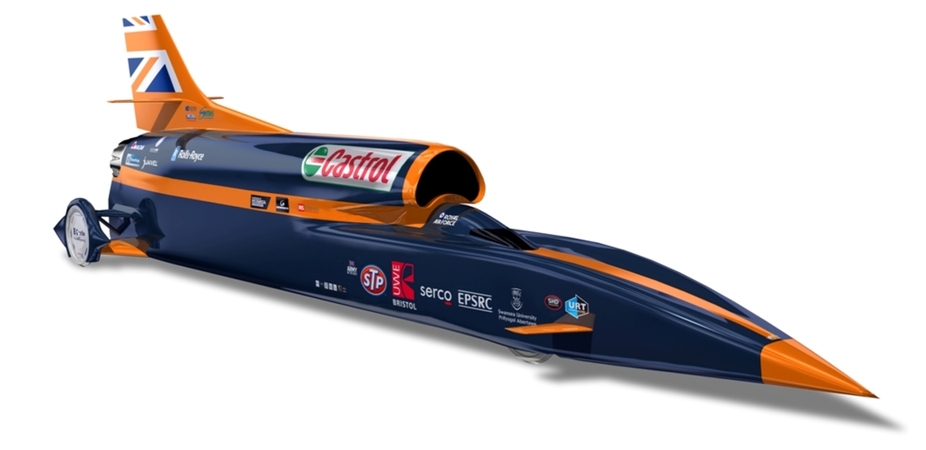
This article was originally published at The Conversation. The publication contributed the article to Live Science's Expert Voices: Op-Ed & Insights.
Apart from a brief break in the 1960s and 1970s, British engineering and drivers have played a dominant role in setting the land speed record in the fastest cars on the planet. Starting from Lydston Hornsted’s Benz No. 3, which broke the record to reach 124mph exactly 100 years ago, to the current land-speed-record holder Andy Green’s Thrust SSC, which crossed the supersonic barrier to reach 763mph in 1997.
Now the people behind Thrust SSC have set themselves an even more challenging target to reach the land speed record of 1,000 mph in a new car called Bloodhound SSC. The target date for achieving it is 2016 and it will be attempted in the Hakskeen Pan in South Africa, where they have created a track that is 12 miles long and two miles wide.
The hope in doing this is to inspire a new generation of British engineers and scientists, promote British engineering around the world and spin out technologies that will affect the design of engineering applications and bolster the UK economy.
How to stay on the ground
It is now seven years since I first sat down with Ron Ayers and Richard Noble, who led Thrust SSC. In that meeting, we discussed the idea and, specifically, aerodynamic challenges of taking a land-based vehicle to 1,000 mph. It was soon after that bizarre encounter that the picture below turned up on my desk at Swansea University (where I was completing a PhD at the time).
A key question when starting to design Bloodhound was: how can we keep the car on the ground? This is important because cars at such speeds are at the risk of taking off, much like how airplanes do. For comparison, a typical passenger plane takes off at about 150mph. Of course the thrust offered to planes is meant for it to take off, but for cars going at 1,000mph, any mistake in the aerodynamics would mean disaster. Although this hasn’t happened in recent attempts of speed records, an example from 1967 when Donald Campbell tried to reach a water speed record illustrates what could go wrong.
Technology developments and the bravery of drivers have kept creating new land speed records all through the last century. Even though the first record was set in an electric powered car, most of the first half of the century worth of records were then dominated by piston engine driven vehicles. These internal combustion engines, as they are known, are found in almost all modern petrol or diesel cars. Using these engines the record could be reached only up to 400 mph.
Get the world’s most fascinating discoveries delivered straight to your inbox.
To push beyond, car builders needed more power. That is when they turned to jet engines and rockets to take over the job of propelling these vehicle. This was also the time when, as speeds kept going up, the resistance caused by air became too important to ignore. Aerodynamics of cars became critical in a successful land speed record attempt.
Faster, stronger, sleeker
Aerodynamics is the study of the flow of air moving over bodies and the forces it induces on that body as a result. The mathematical equations that describe this phenomenon are so complex that until supercomputer arrived, a few decades ago, nearly all aerodynamic studies had to be conducted as experiments in wind tunnels or rocket sled tests.
However, now we are able to get remarkably accurate mathematical models by solving these equations using supercomputers. With greater processing power, computers can run “virtual” wind tunnel testing. The flow must be modelling right down the to chaotic turbulence in the flow happening at tiny length and timescales.
But while working on the problem, we realised that keeping the nose of the car down might not be the real problem. In fact, provided that the height of the nose above the ground is just right we have been able to keep the front of the car almost lift neutral by ensuring that the flow rate under and over the nose is balanced. Instead the problem was keeping the rear of the car on the ground due to the strong shock waves generated by the large, outboard rear wheels and suspension.
This unforeseen aerodynamic behaviour led to the 6-month rear suspension optimisation study that resulted in the “delta fairing” design, recently published in the Journal of Autmobile Engineering. This design effectively protects the base and underside of the vehicle from the high-pressure cushion created on the rear wheel when the car overcomes the sound speed barrier. Without the delta fairing design, the Bloodhound would lift off the ground at approximately Mach 0.9 (90% of the speed of sound), much like Campbell’s vehicle did in 1967.
Feel for numbers
In those early front room conversations we had not anticipated that getting the twin intake bifurcated (split dual intake) duct in the original design to deliver a suitable flow to the EJ200 jet engine compressor face across the entire speed range would be so difficult. This eventually led us to revert to a single intake above the cockpit canopy.
In those early days we had no real “feel” for how stable the car would be, which in turn meant we didn’t really have an idea of how big the fin would need to be to “keep the pointy end pointing forwards” in the words of Andy Green, our driver.
For the first few iterations of aerodynamic design, where we were almost completely focused on the question of what the external shape of the vehicle should be like and still answering trying to figure out if is 1000mph is even possible, we were constantly being surprised by the aerodynamic performance that the computer simulations were predicting. That was not a little nerve-wracking. I would regularly turn up to engineering design meetings, face the rest of the engineers, and my report would be something along the lines of “this is what the simulations are saying… I have no idea why…give me time”.
We have been on quite a journey of engineering design. The image below shows the design evolution from 2007 to the current design (config 12). One thing that you should be able to spot from this view of the design evolution is that as we have been homing in on an optimum shape. The extent of the geometric-shape changes have been getting smaller and smaller. Anyone who has used any form of trial and error, which is essentially what we do in engineering design, will be familiar with this. But, more importantly, what else has been happening is that the aerodynamic effects of making changes to the geometric exterior have become increasingly predictable.
In fact, with the most recent, and subtle, changes to the exterior of the vehicle, Ron and I have been able to confidently predict the impact on aerodynamic performance intuitively and have then used computer simulations check those intuitions. As an aerodynamic designer this is a much happier position to be in.
But as we get close to vehicle testing that is to happen in 2015, the question is going to be whether this predictability will continue. As an academic researcher, hoping to learn as much as possible about the behaviour of computer simulations in extreme applications, in some senses, I hope the answer to that is negative. It would be more interesting to have a new set of questions to puzzle us. But, for now, we must be patient and get Bloohound built. A new land speed record needs to be made.
Ben Evans works for the Bloodhound SSC project.
This article was originally published on The Conversation. Read the original article. Follow all of the Expert Voices issues and debates — and become part of the discussion — on Facebook, Twitter and Google +. The views expressed are those of the author and do not necessarily reflect the views of the publisher. This version of the article was originally published on Live Science.