Breakthrough Makes LED Lights More Versatile
LEDs have started to blink on all over the place in recent years, from car taillights to roadside billboards. But design and manufacturing drawbacks have limited the ways in which the energy-efficient lights can be used.
A new study, detailed in the Aug. 21 issue of the journal Science, tackles these limitations by combining the best of two worlds of LEDs to make ultrathin, ultrasmall and flexible light-emitting diodes that may one day be used to create everything from laptop screens to biomedical imaging devices.
LEDs come in two types: organic and inorganic. Organic LEDs aren't alive, they are just made of organic materials, which means they contain carbon atoms. Inorganic LEDs are more robust and brighter than organic ones, but they're also bulkier as result of how they are put together, explained study leader John Rogers of the University of Illinois.
Rogers and his colleagues first set out to make smaller-sized inorganic LEDs after a request from Ford Motor Co. to create a third brake light for cars that would be a thin strip of red LEDs that conforms to the curves of a car bumper.
"So what we were trying to do really is combine some of the advantages of the processing of the organic devices, with the robustness and brightness of the inorganic" LEDs, Rogers told LiveScience.
Inorganic lights are created by depositing the active material (the chemical compounds that actually emit the light) onto semi-conductor wafers, and the two layers remain attached once the LEDs have been diced up and packaged, making the setup comparatively thick. So it is difficult "to make something that has fine features," Rogers said.
Organic LEDs, on the other hand, can be manufactured so that the active material (which can differ depending on what kind of LED you're making) is put directly onto a piece of plastic or glass and cut by etching, "so you can make displays with millions of pixels" that are much thinner, Rogers said.
Get the world’s most fascinating discoveries delivered straight to your inbox.
Rogers and his team developed a process in which the active material, though inorganic, is grown on a wafer, as before, but this time between the two is a "sacrificial layer" which can be etched out in a chemical bath, lifting the active layer away from the wafer. The active layer can then be etched into smaller squares and picked up by a rubber stamp and stamped onto plastic or glass.
"As a result our devices are much, much thinner," Rogers said. They're also hundreds to thousands of times smaller — about one or two microns (or the width of a couple human hairs) instead of about 0.5 millimeters (or the size of a mosquito's body) — allowing for finer resolution in the final LED display — a key criteria for high-definition TVs and medical devices.
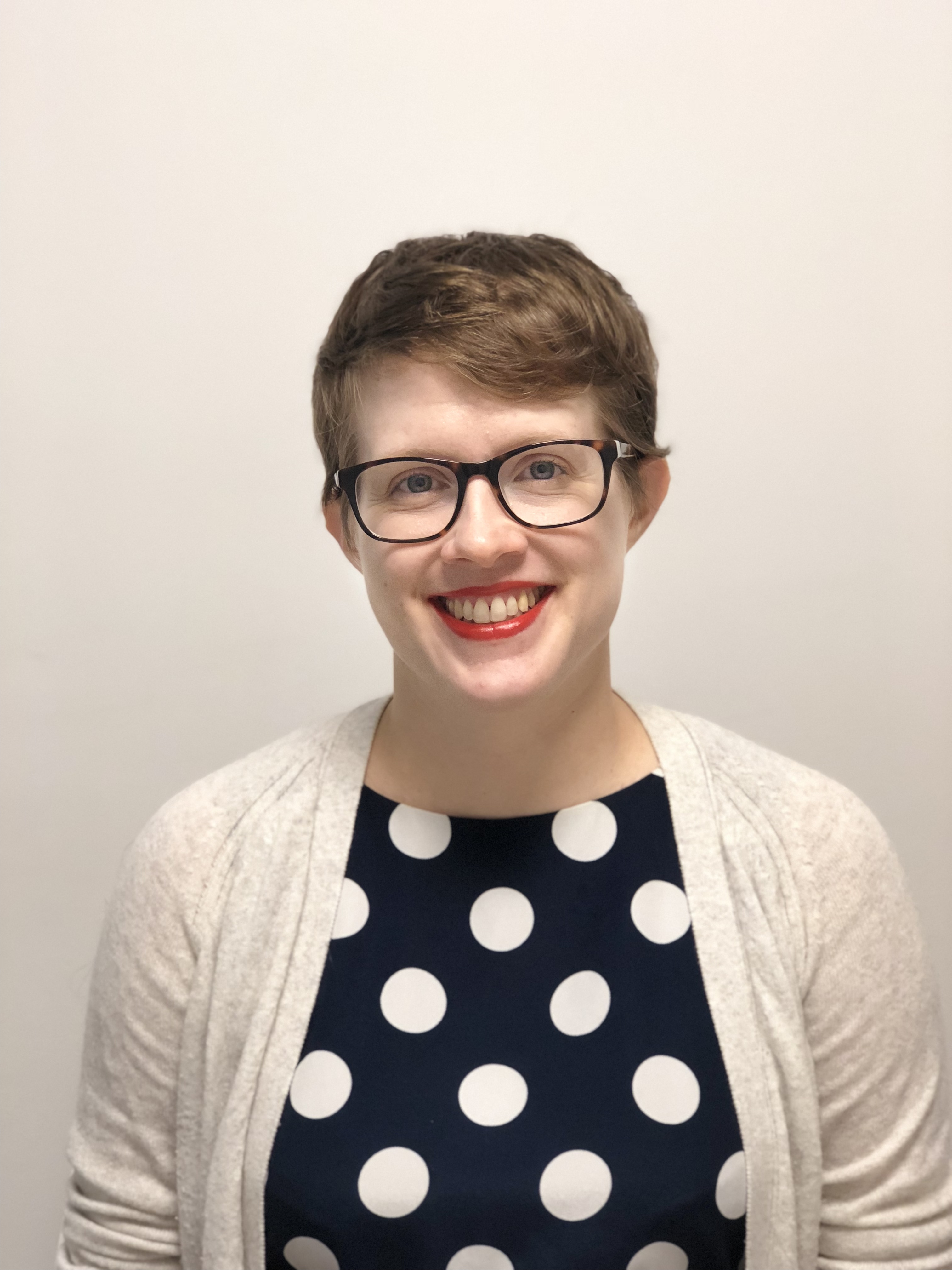
Andrea Thompson is an associate editor at Scientific American, where she covers sustainability, energy and the environment. Prior to that, she was a senior writer covering climate science at Climate Central and a reporter and editor at Live Science, where she primarily covered Earth science and the environment. She holds a graduate degree in science health and environmental reporting from New York University, as well as a bachelor of science and and masters of science in atmospheric chemistry from the Georgia Institute of Technology.