Robotic Systems Help People with Disabilities
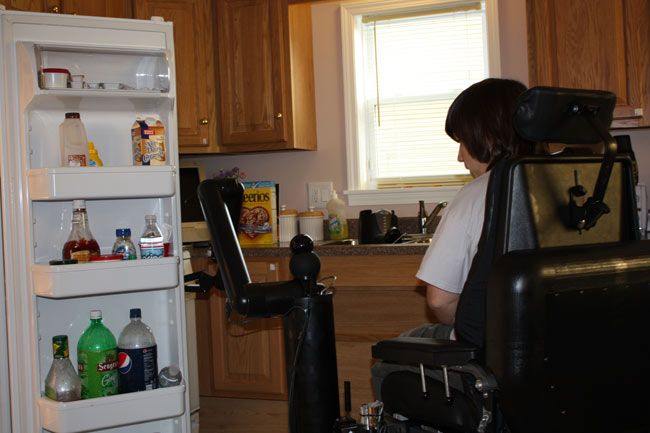
This Behind the Scenes article was provided to LiveScience in partnership with the National Science Foundation. People might be surprised to learn that about 50 million people in the world use, or could benefit from the use of, a wheelchair. Wheelchairs are one of the most commonly used assistive devices for mobility, and they provide people with mobility within their homes and communities. While wheelchairs were once a symbol of inability and stigmatizing, they have evolved to be highly mobile forms of self-expression that are often fitted to each individual user. One may wonder what science and engineering can do to improve the wheelchair, and be surprised by the answer that much has been and remains to be done. One of the areas in which science and engineering are making the breakthroughs of tomorrow is in applying computer modeling, rapid-prototyping and robotics to create electric powered mobility and manipulation devices. Such devices provide people with very severe disabilities — those that affect both the use of their arms and legs — the ability to perform tasks with minimal assistance or even independently. Computer modeling allows engineers to design and simulate such systems within a virtual space. Simulations range from the mechanical and circuit design to the complex control and coordination systems needed to make all of the components work together. One of our greatest challenges is ensuring that the powered mobility and manipulation device actually meets the user’s needs, and that the science is guided by problems facing people with disabilities. In our work, we collaborate closely with people with disabilities and incorporate them into our research and development team. These collaborators highlight some of the hurdles that they face, and other potential uses of powered mobility and manipulation devices, such as driving on rough terrain like snow, ice, grass, sand and gravel. For people who have limited or no use of their arms, it is equally as challenging to complete such tasks as making a sandwich, putting away clothes, and shopping. Many people would like to drive the powered mobility device in parks, on winter days or across gravel roads, which is difficult and sometimes impossible with the technology of today. Likewise, people with some severe disabilities require a person to help them perform tasks, such as adjusting their jacket, which many of us take for granted. Rapid-prototyping and robotics provide some promising solutions to at least some of the challenges faced by people with severe mobility and manipulation, and offer hope for greater independence. Rapid-prototyping helps engineers to make models and even one-off devices in a cost effective and timely manner. This allows computer models to become physical models within days, and real systems within months rather than years. This accelerates the research and design process, and affords people with disabilities more opportunities to participate in the scientific process. Robotics has traditionally focused on replacing humans in the performance of tasks to achieve greater efficiencies or to reduce human exposure to risk. In our work, the person and robot must work together in what we call cooperative control. In our cooperative control model, we have a pilot who is the actual person with a disability, a remote human assistant, and the robotic system. With cooperative control these three core units work in unison to achieve the actions desired by the pilot in natural environments. This approach speeds deployment from the laboratory into the real-world, and allows scientists and people with disabilities to learn from each other throughout the process, to work towards achieving practical robotic mobility systems that safely, effectively, and efficiently help people with disabilities perform the activities that they desire. To read more about these projects, visit the website for NSF’s Quality of Life Technology Center
Editor's Note: This research was supported by the National Science Foundation (NSF), the federal agency charged with funding basic research and education across all fields of science and engineering. See the Behind the Scenes Archive.
Get the world’s most fascinating discoveries delivered straight to your inbox.