3D-Printing a Low-Cost Satellite
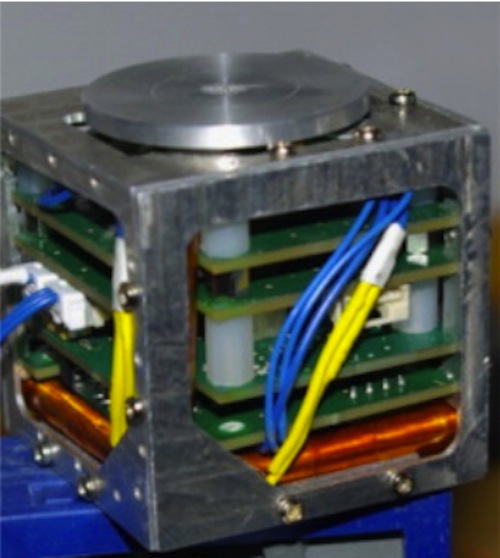
Seeking a low-cost way to launch their experiments into space, a team of scientists has designed a space-ready, 3-D printed CubeSat.
CubeSats are standardized, tiny satellites, often only 10 centimeters (3.9 inches) on each side and weighing less than 1.33 kilograms (just under 3 lbs). They are so small that they have room for only a few sensors, and burn up in the Earth's atmosphere after just a few months. Kits cost under $10,000, which is considered cheap for the space industry. But Jacopo Piattoni of the University of Bologna and his team aim to drive the satellites' price down even further, while making the devices easier to customize.
In 3D printing, a computer-directed nozzle "prints" a three-dimensional object in plastic. Often, engineers use this method to design a prototype for a product that will then be built out of metal or another, sturdier medium. But Piattoni’s team hopes their plastic CubeSat could survive launch and low-Earth orbit.
Using 3-D printers, researchers can automate the CubeSat production process. “We don’t need a technician,” Piattoni said, adding that this also makes the process faster.
[NASA Turns to 3D Printing for Self-Building Spacecraft]
The CubeSat’s sensors and computer chips, of course, weren't printed in the lab, and the team had to add a small, metal heat sink to disperse the electronic components' heat. The method holds promise, though. When the researchers tested the chassis in near-space conditions, "it did really well," Piattoni said.
Piattoni chose ABS plastic, the same type of plastic used in Lego bricks, to construct his CubeSat because of that material's resilience to extreme temperatures, vibrations, radiation and more. A satellite will absorb a lot of solar radiation during its spaceflight, and its temperature will swing from -4 degrees F (-20 degrees C) to 176 degrees F (80 degrees C) each orbit. "It's not so easy for plastics in that environment," Piattoni said.
Get the world’s most fascinating discoveries delivered straight to your inbox.
In fact, ABS plastic was famously indicted in a massive seat-belt buckle recall in the mid-90s because UV radiation weakened buckles made from the material. But such radiation, even at elevated levels, won't pose a problem for the CubeSat, due to its short lifetime.
With one successful satellite constructed, the team can now use the 3-D printer to crank out another copy each night. They can also test new designs or build support for other sensors or modules, just by clicking a few buttons on a computer.
The final product passed its tests with flying colors. Now, like most other CubeSats, it will hitch a ride into space as secondary cargo on a rocket already headed to its preferred orbit. Piattoni's team is working with QB50, which will put 50 CubeSats into orbit at once on a Russian Shtil-2.1 scheduled to launch in 2014.
The satellite was designed and tested by Piattoni and researchers in the University of Rome's Department of Astronautical, Electrical and Energy Engineering and the Department of Mechanical and Aerospace Engineering.
This story was provided by TechNewsDaily, sister site to LiveScience.
Rachel is a writer and editor based in Washington, D.C., who covers a range of topics for Live Science, from animals and global warming to technology and human behavior. Rachel also contributes to National Geographic News, Smithsonian Magazine and Scientific American, and she is currently a senior editor at Next City, a national urban affairs magazine. She has an English degree with a journalism concentration from Adelphi University in New York.