In Structural Design, Less is More
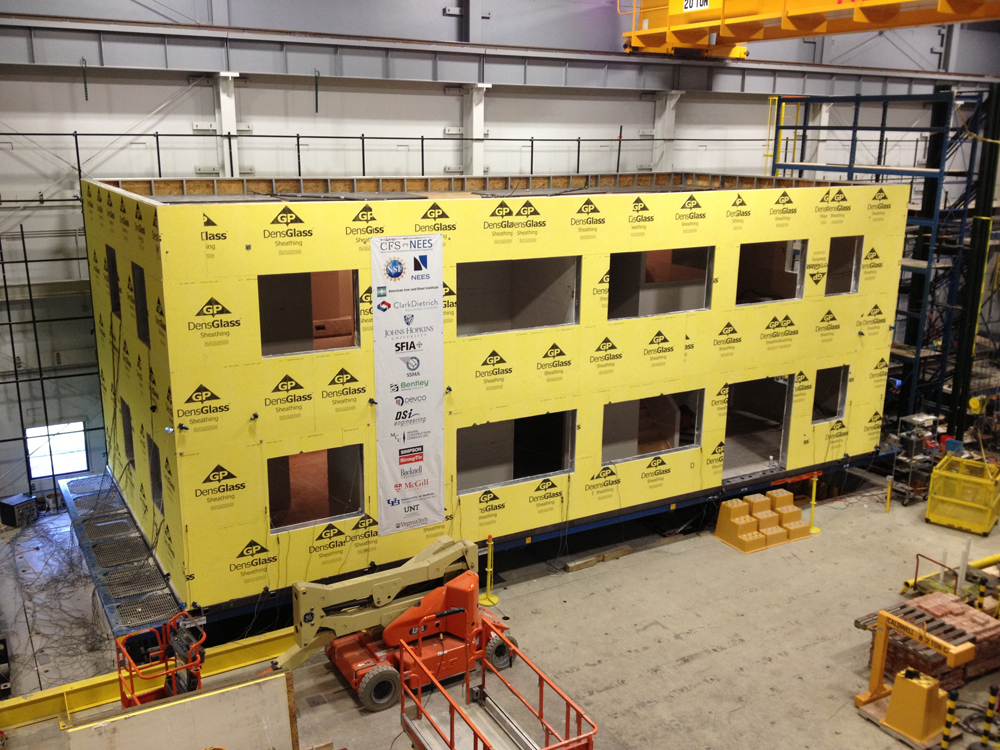
This Behind the Scenes article was provided to LiveScience in partnership with the National Science Foundation.
If I asked you to design a building to withstand unknown forces, what would you do?
You might either throw your hands up and walk away, the uncertainty too insurmountable, or proceed to build the strongest, heaviest structure you could. If I then told you specific forces to design for, say, 50 mph winds and magnitude 6.9 earthquakes, you might revisit your strong, heavy design and examine what parts are unnecessary. Do you really need walls that are three feet deep?
This is the essence of modern structural engineering. The more you know about your force demand, the better you can refine your structure's capacity to meet those demands. Less (when designed efficiently) is more.
Very broadly, this is what my research aims to accomplish: efficient structural design. My particular field is cold-formed steel, a building material that is formed by rolling steel into thin sheets, then folding it into efficient shapes to make beams and columns. Cold-formed steel, like all building materials, is designed via a set of rules referred to as building codes. These ensure that all buildings are designed to be safe for their occupants, whether a hospital, house or skyscraper.
Build your own earthquake
Obviously, safety is the most important factor in building design. Probably the second-most important factor is cost. If a good engineer can design a safe building that costs half the price, why pay more?
The cold-formed steel building code for earthquake forces is rather thin, and rife with conservatism, due to an overall a lack of information about how cold-formed steel buildings respond to earthquakes. One way to obtain more information about such responses would be to build a cold-formed steel building, and wait for an earthquake to come along.
Get the world’s most fascinating discoveries delivered straight to your inbox.
However, thanks to the Structural Engineering and Earthquake Simulation Laboratory at the University at Buffalo, there is no need to wait for an earthquake — one can easily be created in the lab! These earthquake simulators, or shake tables as we call them, are large platforms on which full-scale buildings can be constructed and shaken. We took advantage of these shake tables and built a cold-formed steel building on top of them.
Crazy as this sounds, it worked.
It showed us how a cold-formed steel building behaves under a magnitude 6.9 earthquake, and provided us with information that enables us to determine how various parts of the building transfer forces, and how components such as drywall, interior walls, staircases and weatherproofing add to the building performance.
Designed for maximum safety
There are still reams of data to wade through, but one interesting outcome was how well our building performed. We shook the building with two earthquakes — one called a design basis earthquake that the building was designed to withstand with no or minimal damage, and the other called the maximum considered earthquake that the building was not designed to withstand.
What is the difference between the DBE and MCE? The MCE is significantly stronger than the DBE, and is quite rare. Typically, there is a significant amount of damage after an MCE, though no collapse; the structure remains upright so the occupants can safely evacuate.
But in our tests, the building exceeded expectations and sustained only a small amount of damage after the MCE. This is great! Safe structures for everyone!
However, this leads back to the idea of efficient design. Now that we know how a cold-formed steel building stands up to a strong earthquake, how can we improve design and make structures more efficient? The more you know…
Editor's Note: The researchers depicted in Behind the Scenes articles have been supported by the National Science Foundation, the federal agency charged with funding basic research and education across all fields of science and engineering. Any opinions, findings, and conclusions or recommendations expressed in this material are those of the author and do not necessarily reflect the views of the National Science Foundation. See the Behind the Scenes Archive.