Spider Silk-Spinning Technique Key to Stronger Fibers
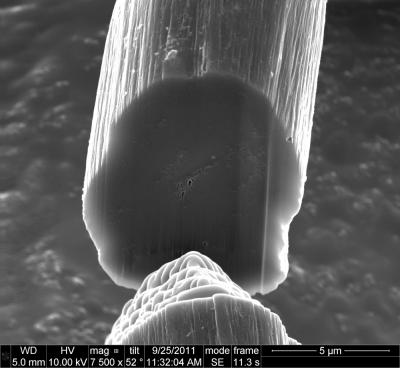
Mimicking silk-spinning spiders, scientists have created a type of nanotube fiber with an unmatched combination of strength, conductivity and flexibility.
These light, versatile fibers could find uses in the aerospace, automotive, medical industries, as well as the smart-clothing markets, researchers say.
Carbon nanotubes arehollow tubes of pure carbon just nanometers or billionths of a meter in diameter. Although they are only about the width of a strand of DNA, they are about 100 times stronger than steel and only one-sixth as heavy, and their conductive properties for both electricity and heat rival the best metal conductors ―enthralling qualities that have attracted much interest from researchers since they were discovered in 1991.
With all their vast potential, however, carbon nanotubes are extremely difficult to work with, and creating carbon fibers that retain the startling qualities of the nanotubes themselves has proved highly challenging.
There are two strategies researchers have pursued to make carbon nanotube fibers. One route, known as the solid-state processes, involves taking the dry, hairball-like clumps that nanotubes typically form and spinning threads from them much as one would from balls of cotton. The other, known as wet-spinning, involves taking a stream of fluid containing the nanotubes and coagulating it to create a solid fiber, much the same way spiders generate strands of silk.
[New Worms' Silk Has Spider Strength]
The carbon fibers with the best mechanical and conductive properties are theoretically those with tightly packed and perfectly aligned nanotubes, like pencils in a box. Since solid-state processes start with entangled masses of nanotubes, the resulting fibers are often relatively disorderly and loosely packed, and spinning fibers from these clumps can be awkward and cumbersome, making it hard to scale up to industrial levels.
Get the world’s most fascinating discoveries delivered straight to your inbox.
Despite these shortcomings, solid-state carbon nanotube fibers have delivered the best properties so far, because they can use relatively long carbon nanotubes, measuring a millimeter or more.
In comparison, wet-spinning is relatively simple, making it easy to scale to industrial levels. It also has the benefit of forming the most highly ordered and dense carbon nanotube fibers. However, wet-spinning has long worked only with carbon nanotubes about a half-micron long — that is, half a thousandth of a millimeter long, or about 200 times smaller than the thickness of the average human hair. These have disappointing mechanical and conductive properties compared with their longer brethren.
"Nanotubes really like each other, and tend to entangle and stick, and as they get longer and longer, their surface interactions get stronger and stronger, and if you want the benefits that come with using carbon nanotubes, you want them ordered, not entangled," researcher Matteo Pasquali, a chemical engineer at Rice University in Houston, told TechNewsDaily.
Now Pasquali and his colleagues have discovered a way to wet-spin fibers using carbon nanotubes 10 times longer than before.
"We finally have a nanotube fiber with properties that don't exist in any other material," Pasquali said.
The secret of the new technique is dissolving the nanotubes in a very strong acid, chlorosulfonic acid. This tames the surface properties of carbon nanotubes, helping keep relatively long carbon nanotubes from entangling.
"A graduate student in my lab, Natnael Bahabtu, found simple ways to show that carbon nanotube fibers could be spun from chlorosulfonic acid solutions," Pasquali said. "That was critical for this new process."
The new fiber, which is about 10 to 50 microns wide, contains tens of millions of nanotubes packed side by side.
"It looks like black cotton thread but behaves like both metal wires and strong carbon fibers," Pasquali said.
The new fibers have about 10 times the tensile strength and electrical conductivity of the best previously reported wet-spun carbon nanotube fibers, and 30 times the thermal conductivity. When compared with the best solid-state fibers, they are about a match in terms of tensile strength, three to five times better in electrical conductivity, and 10 times more thermally conductive.
"The new carbon nanotube fibers have a thermal conductivity approaching that of the best graphite fibers but with 10 times greater electrical conductivity," said researcher Marcin Otto, business development manager at the Dutch firm Teijin Aramid. "Graphite fibers are also brittle, while the new carbon nanotube fibers are as flexible and tough as a textile thread."
The electrical conductivity of the new fibers is on par with copper, gold and aluminum wires, but the new material is stronger and lighter.
"Metal wires will break in rollers and other production machinery if they are too thin," Pasquali said. "In many cases, people use metal wires that are far [thicker] than required for the electrical needs, simply because it's not feasible to produce a thinner wire. Data cables are a particularly good example of this."
"In theory, we should be able to increase strength up to a factor of 10 to 30 times; electrical conductivity by a factor of 10 to 20 times; thermal conductivity by a factor of five to eight times," Pasquali said. "We hope to improve properties by using longer, more perfect carbon nanotubes, potentially ones that are all identical to each other and have the same atomic configuration along their length and have only a single wall of carbon. We also hope to improve properties by improving several steps of our spinning process and post-processing."
The scientists detailed their findings in the Jan. 11 issue of the journal Science.
This story was provided by TechNewsDaily, sister site to LiveScience.
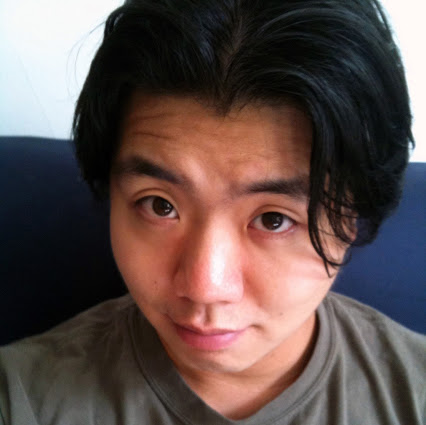