
Black to the Future: Carbon Fiber Research Seeds New Innovation (Op-Ed)
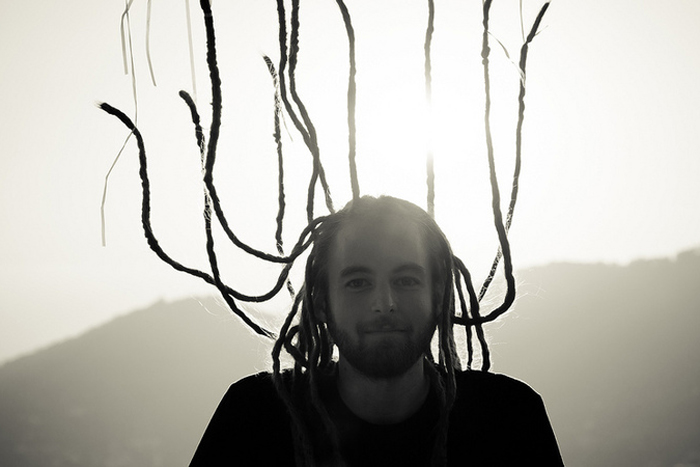
This article was originally published at The Conversation. The publication contributed the article to Live Science's Expert Voices: Op-Ed & Insights.
A unique cutting-edge carbon fibre research facility Carbon Nexus officially opened at Deakin University in Geelong last week. It houses laboratories, a pilot scale carbon fibre line and a smaller single-tow research line.
But what is it about carbon fibre that gets researchers – and investors – so excited?
Carbon fibres can be made from a number of starting materials including coal tar “pitch” (a side product of petroleum distillation) and rayon, but most commercial carbon fibres are made from a polymer called polyacrylonitrile or PAN.
PAN begins its life as a powder of the polymer building blocks (acrylonitrile), which is then mixed with a catalyst in a solution. Over a short period of time the building blocks start joining to form long chains of white polymer. These are then collected by a system of rollers which lead the fiber through the production line.
The fibre passes through series of washing, stretching, relaxing and drying steps all while making one long, continuous bundle. The result is a spool of incredibly fine white PAN fibre between 1,500m and 3,000m long.
This PAN fibre is then converted to carbon fibre by feeding the spool through three different ovens. The high temperature treatments have a very special role to play in the chemistry of the fibres.
Get the world’s most fascinating discoveries delivered straight to your inbox.
PAN has a mixture of carbon, nitrogen, oxygen and hydrogen atoms, which results in a flexible and stretchy fibre, but to achieve the high strength properties of the final carbon fibres all non-carbon atoms must be removed.
As the spool is unwound and the PAN fibres pass through ovens with strictly controlled pressure and temperature, the heat energy causes the carbon atoms in the fibre to link together, and all other atoms evaporate as gases. It is these long chains of joined carbon atoms which give carbon fibres their incredible strength properties.
The final steps in the process (oxidation and “sizing” which involves painting on a thin layer of resin) have the dual purpose of improving the way the fibres perform in a composite, and helping them stick together so they can be easily weaved into a carbon fibre mat.
Strength in fibres
Carbon fibre composites, which are weaved carbon fibres coated in hard polymer resin, are increasingly used across a vast range of industries.
In aerospace, automotive, oil and gas they are replacing traditional materials such as steel and aluminium.
The reason carbon fibre composites are becoming the forefront of new materials technology are their unmatched strength to weight ratio, making them as strong as steel while only a fraction of the weight. By changing the type of polymer matrix and the layers of carbon, they can outperform steel or aluminium in durability.
This durable, strong and lightweight material has already made a significant contribution to sporting equipment such as bikes and golf clubs.
Alongside Carbon Nexus at the Waurn Ponds Campus is Carbon Revolution which produces the world’s first high performance wheels for high performance cars made from one piece of moulded carbon fibre.
(The new production facility has led to the investment of A$23.8 million and creation of 150 jobs in a collaboration with local and international businesses.)
Because carbon fibre is weaved into a flexible mat before it is covered in a hard resin layer, it is very easy to mould into complex shapes. Carbon Revolution uses special techniques to mould carbon fibre into a solid wheel, which is then covered in resin and cured to give the final product.
There are also large implications in terms fuel efficiency. Carbon fibre composite materials make up 50% of Boeing’s 787 Dreamliner, helping to achieve a 20% improvement in fuel economy and reduction in greenhouse gas emissions.
Global carbon fibre demand is forecast to increase at an annual rate of 13-17% and the market for carbon fibre reinforced composites is predicted to increase from US$14 billion in 2012 to US$36 billion in 2020.
Carbon fibre has a number of other applications which may be less obvious. Strips of carbon fibre have even been used to increase the load bearing capacity of the West Gate Bridge in Melbourne.
The value and potential of carbon fibre composites in future technologies has sparked worldwide interest in carbon fibre research. New research being conducted focuses on low-cost fibres, high performance fibres, surface treatments and advanced composite manufacturing to make next generation materials.
There are enormous opportunities for Australia to participate in this rapidly growing sector and a number of Australian companies successfully doing this already include Quickstep Technologies, Morand, CST Composites and Carbon Revolution.
Linden Servinis receives funding from the Australian Future Fibres Research and Innovation Centre.
This article was originally published on The Conversation. Read the original article. Follow all of the Expert Voices issues and debates — and become part of the discussion — on Facebook, Twitter and Google +. The views expressed are those of the author and do not necessarily reflect the views of the publisher. This version of the article was originally published on Live Science.