Future Aircraft Could Repair Themselves
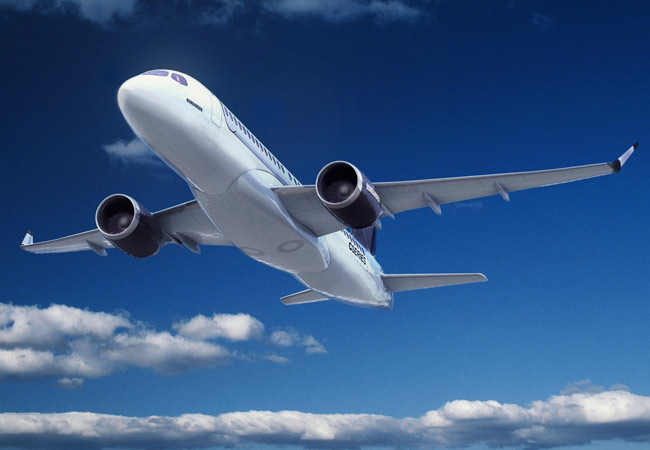
Damaged aircraft could repair themselves automatically, even during flight, by mimicking healing processes found in nature, a researcher said this week.
One method could be as simple as a resin that oozes into cracks on demand.
Not only might such a breakthrough lead to safer planes, but it could also lead to lighter craft that would save fuel, drop costs and reduce global warming gas emissions as well.
"At oil approaching $130 a barrel, if you can strip weight off, you could save money," said researcher Ian Bond, a materials scientist at the University of Bristol in England.
Damage common
Aircraft routinely suffer damage from day-to-day use. A great deal of aerospace research goes into materials that can resist damage.
"You would be surprised how often trucks drive into aircraft when parked at airports," Bond told LiveScience. "And then you have tools dropped on planes at maintenance hangers, or hailstones when flying through storms. Very subtle damage, little dings and cracks and bangs that, if left undetected, could grow into something serious. At aircraft hangers, a lot of time is spent trying to find these defects."
Get the world’s most fascinating discoveries delivered straight to your inbox.
Aircraft designs that nowadays help cope with damage end up adding weight.
"The idea is that you'd want what structure you'd have left after damage to be able to sustain all the loads you'd be likely to see," Bond said. "This ends up adding weight, which as you can imagine is at a premium with aircraft."
Humans do it
A system that could help planes repair themselves "would definitely help with safety, and by not worrying as much about damage, there could be huge savings in weight," Bond said. "The human body repairs itself all the time, sometimes after quite severe damage. Why can't we make structures do the same sort of thing?"
The key would be hollow fibers loaded with epoxy resin and hardener. Such vessels could be embedded in any part of the structure of the aircraft — its fuselage, wings, nose or tailfin — and would bleed out when cracked to seal any hole, mimicking scabs over a wound. The damaged material could recover up to 80 to 90 percent of its original strength, comfortably allowing a plane to function.
Dye mixed into the resin could make repaired damage show up as colored patches that could easily be spotted during subsequent ground inspections, so that full repairs could be carried out if necessary. Such dye would not show up in normal lighting conditions, only visible when exposed to ultraviolet light. This way, the system will "complement rather than replace conventional inspection and maintenance routines, which can readily pick up larger-scale damage, caused by a bird strike, for example," Bond said.
These resin-loaded fibers could find use wherever fiber-reinforced polymer composites are used. Such lightweight, high-performance materials are proving increasingly popular not only in aircraft but also in cars, wind turbines and even spacecraft. The new self-repair system could therefore have an impact in all these fields.
Circulating scheme
The scientists are also developing systems where the healing agent is not contained in individual fibers, but can actually move around in a network of tubes, "just like the circulatory systems found in animals and plants," Bond said.
"Such a system could have its healing agent refilled or replaced and could repeatedly heal a structure throughout its lifetime," he added. "Furthermore, it offers potential for developing other biological-type functions in man-made structures, such as controlling temperature or distributing energy sources."
Currently Bond and his colleagues are working with hollow glass fibers loaded with an off-the-shelf resin. They are currently developing a custom-made resin optimized for use in the system.
"Current epoxy systems have to be mixed in precise ratios, such as two parts of one ingredient with one part of another," Bond said. "We'd need the resin to be much more tolerant of different mix ratios, because we can't control the situation in the air."
"And we'd need it to be low viscosity, and fairly stable — it needs to last a long time," he added. "It could be sitting in an aircraft's structure for quite long periods of time, maybe years, and still needs to be reactive when called upon."
The resin would need enough time to ooze into any crack before hardening, yet ideally work quickly enough to have an effect when the aircraft is still flying. Control of the hardening of the resin would get complicated by the cold temperatures found in the high altitudes that planes typically fly at.
"I think such a resin is achievable," Bond said. "It's just that no one's ever been asked to make such a resin."
A working system could be up in the next five years, Bond suggested.
The scientists received funding from the United Kingdom's Engineering and Physical Sciences Research Council.
- Time Travel: Is It Possible?
- Quiz: The Greatest Inventions
- How Planes Fly
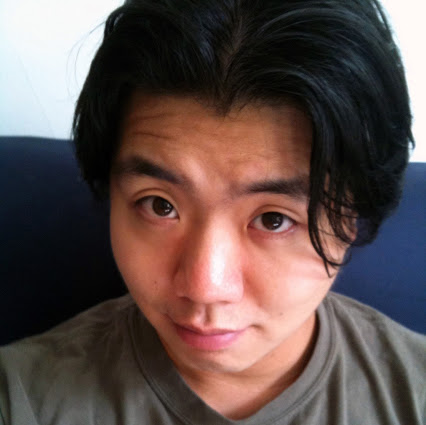