
Elastic to Plastic: High-Energy Lasers Warp Copper – Permanently (Op-Ed)
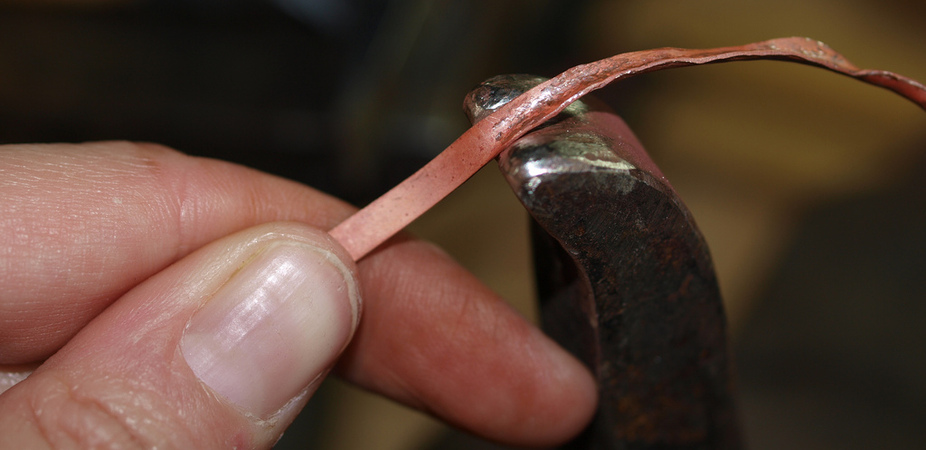
This article was originally published at The Conversation. The publication contributed the article to LiveScience's Expert Voices: Op-Ed & Insights.
The exact pressure that permanently changes copper crystals has been pinpointed, according to a study released today.
The findings, published in the journal Science, show that when copper is compressed the microscopic building blocks of the crystals undergo two types of change.
A better understanding of these changes will enable scientists to optimise the properties of complex materials such as those used in aeroplanes, cars and some machines.
Using ultrafast X-ray diffraction, which are pulses of X-ray probes generated at extremely short durations and intervals, the researchers fired high-energy lasers at the copper crystals to compress them.
“Think of a hammer applying pressure on the copper sample one million times the atmospheric pressure, within about 80 trillionths of a second,” said Despina Milathianaki, a scientist from Stanford University and the study’s lead researcher.
The researchers then took snapshots of the crystals in very quick succession (120 shots per second) to closely observe the transformations that occurred at an atomic level.
Get the world’s most fascinating discoveries delivered straight to your inbox.
In general, materials respond to forces of stress by compressing and then returning to their original shape. This response is called an elastic response and takes place up to a certain threshold.
Once that threshold is reached, any change that occurs to the material now becomes permanent. This is known as the plastic response.
In this study, the researchers closely observed the way a pure copper crystal deformed under pressure by noting any distortion (that is bending, stretching or twisting) to its regular 3D lattice of atoms.
Tim Davis, principal research scientist of materials science and engineering with CSIRO, said the positions of the atoms could be worked out from the way in which X-rays scatter from them.
“If the atoms are in a regular pattern, you will see a regular and symmetric pattern of X-rays after they have passed through the crystal. As the crystal distorts, the atoms move away from their regular positions, which is seen as distortions in the X-ray pattern.
“A high intensity laser pulse applied to the crystal compresses it very quickly, after which it will spring back into its original position, so using a rapid sequence of X-ray pulses enables the researchers to see how the copper atoms respond in time to the compression and move back into their regular positions.
“If the atoms move beyond their elastic limit, they can no longer move back into their regular positions – the crystal structure is broken.”
According to David Reis of Stanford University it’s the first time researchers have been able to view the elastic to plastic transition in real-time with atomic-scale resolution.
Led by Dr Milathianaki, the study was conducted by a team of staff scientists from the National Accelerator Laboratory’s Linac Coherent Light Source (LCLS) at Stanford University and collaborators from Oxford University, Stanford University and Lawrence Livermore National Laboratory.
Amanda Barnard, leader of CSIRO’s Virtual Nanoscience Laboratory, said the method could be used to examine the nature of metal fatigue and corrosion – allowing scientists to determine the effectiveness of protective coatings used in the aerospace industry.
This article was originally published at The Conversation. Read the original article. The views expressed are those of the author and do not necessarily reflect the views of the publisher. This version of the article was originally published on LiveScience.